Zero Discharge & Water Recycling Becoming a Necessity
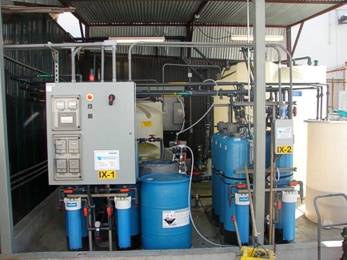
Wastech dual train DI skid with automated controls
The Drought is Back! If you are located in the Southwest, you are already aware of the pending water disaster. If your plant uses water, you must address this growing problem, or your plant's survival may be at stake. Industrial customers have been feeling financial pressures for years with rising water costs and increasingly costly discharge fines, but it is no longer a cost issue alone. New regulations and possible water rationing now demand water conservation to cope with reduced supplies. We have seen reductions in discharge permit volumes over the past few years, sometimes without warning. Waste hauling charges are growing exponentially, and we can no longer take waste disposal for granted.
A Zero Discharge Program is the answer, as more and more accounts want to eliminate industrial discharge permits completely and recycle all water used in their facility (excluding sanitary waste). Facility managers, plant managers, board of directors and owners want help. This topic opens doors and draws a crowd.
Wastech engineers have the experience to solve water recycling issues. Whether automating a waste water system or designing a complete zero discharge program, Wastech can offer a turnkey solution. Wastech engineers are integrators – they are not beholden to any supplier – they will analyze your water needs, develop a process plan and help you write a performance specification that will work. Don't be fooled that water recycling is a hardware issue. It never is. Addressing hardware alone will result in costly mistakes and damaged reputations.
A zero discharge, water recycling example is the recent decision of an aerospace metal fabricator with in-house plating, etching and anodizing operations. The plant used a large volume of DI water, and the DI suppliers were charging monthly to service DI resin regeneration. In addition, rinse tanks were neutralized and dumped to the sewer along with other industrial wastewater. Some concentrated heavy metal waste was hauled away. Rising DI service costs and hauling expenses along with NOVs (Notice of Violations) for pH excursions caught the attention of management.
Wastech engineers evaluated the problem and suggested several options that surprised the facility engineer, generated a management presentation and resulted in a larger and more successful project than was first anticipated. The result was a new Wastech DI system with on-site resin regeneration, plus a Wastech vacuum distillation for waste reduction and distilled water production. An adequate supply of DI water was generated on-site, wastewater was recycled, and a only a small amount of concentrated waste had to be hauled.
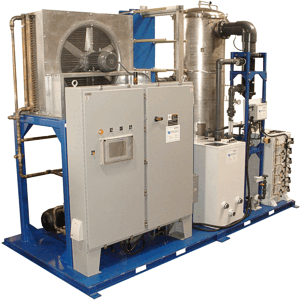 Sigma VDT2000 vacuum distillation unit
The cost savings were substantial, and the need for new water was reduced as the plant converted to zero discharge. Contaminated water that had been hauled could now be treated on site. Recycled distilled water could be used in the rinse tanks and in parts washing operations. Clean water could be generated from wastewater in an automated system that required minimal operator attention. Best of all, zero discharge could be accomplished, eliminating significant liabilities to the plant and the annoying and risky regulatory inspections associated with industrial discharge permits.
|