PROCESS SUPPORT SYSTEMS FOR THE PHOTOVOLTAIC SOLAR CELL MANUFACTURING INDUSTRY
A white paper by Wastech Controls & Engineering, Inc.

High Purity Chemical Delivery Modules (CDM) deliver electronics grade chemicals from supply drums, totes or tanks to process tools located in the facility. These fully contained pump cabinets provide safe, reliable operation while preventing personnel exposure to corrosive or toxic chemicals. They feature welded polypropylene cabinets equipped with single or multiple air operated pumps. The supply and discharge tubing, fittings and wetted parts of instruments and pumps are constructed of Teflon® to assure the purity of delivered chemicals. CDM's are available for HF, HCl, NaOH, KOH, BOE, HNO3, H2SO4, H2O2, NH4OH, IPA and other chemicals on request. |
Design Criteria (standard system):
- Simplex High Purity Air Operated Pump (e.g. Trebor or Yamada)
- 1-20 gpm flow rate at 10-75 psig
- PFA (i.e. Teflon®) wetted components
- 1 micron filter
- Welded polypropylene cabinet
|
Configuration Options:
- Duplex Pumps
- Alternate OEM Pumps and wetted materials to match chemical compatibility
- Automatic air purging
- Nitrogen blanket pressure regulator and flow controls
- Pump operation on permissive/demand signal or pressure control
- Constant flow with backpressure control and return to the supply container
- Valve Manifold Boxes (VMB) for branch distribution within Fab area
- Stainless steel fabrication for solvents such as IPA
Control System Options:
- Programmable Logic Controller (PLC) or Relay Controls
- Pump permissive dry contacts for interlocks with upstream equipment
- Integrated controls for CDM and downstream VMB
- Safety alarms for open doors, leak containment, low and high pressure, proof of flow, and others
- Automatic supply pressure control
- Common trouble alarm dry contacts for remote alarm notification
- Ethernet LAN communication for PLC controls
- Building Management System (BMS) integration
Pump Lift Stations are used to transfer process tool waste water from gravity-fed drain lines to treatment systems downstream. The lift stations may be located close to process tools, or remote from the fabrication area in a facility vault or yard area. The tank, pump and piping materials selection will be matched to the expected process conditions.
Pump Options:
- Air Operated Diaphragm Pump
- Vertical or Horizontal Centrifugal
- Simplex or Duplex Configurations
Tank Options:
- Tank capacities from 16 gal to 2,000 gal
- Single Tank or with Secondary Containment Tank
- Molded or fabricated plastic tank construction (PP, PE, PVDF, PVC or CPVC)
- Stainless Steel Construction
- With or without valve manifold enclosures
Control System Options:
- Level point switches or continuous transmitters
- Local or remote control panel
- Upstream and downstream permissive signals
- Flow and pressure indicators and/or transmitters
- Secondary containment leak alarm
Process Cooling Water (PCW) provides cooling to heat exchangers within process tools to regulate operating temperatures. Process tools require purified water (i.e. either reverse osmosis (RO) or de-ionized (DI) quality) as a medium for cooling to avoid product or tool contamination in the event of a heat exchanger leak. Wastech builds PCW skids that include the pumps, filters, heat exchangers and controls to supply cooling water at the flow rate and temperature required by the facility. The PCW fluid is cooled by heat exchange with the facility's chilled water system.
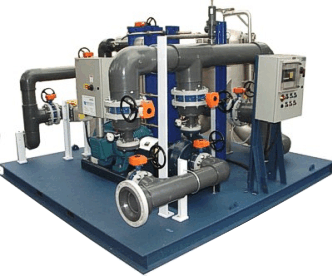
Configuration Options:
- Flow rates from 50 gpm to 2,400 gpm
- Supply pressures from 20 psig to 110 psig
- Multiple redundant stainless steel pump arrangements
- Variable Frequency Drive (VFD) pump control
- Stainless steel plate and frame heat exchangers
- 20 micron filter unit
- Sch 80 PVC or Stainless steel piping
- Nitrogen blanket pressure regulator and flow controls for vented systems
- Expansion tank for closed systems
- Powder-coated structural steel skid
Control System Options:
- Programmable Logic Controller (PLC) or Relay Controls
- Automatic supply pressure and temperature control
- Common trouble alarm dry contacts for remote alarm notification
- Ethernet LAN communication for PLC controls
Process Hot Water provide hot water in a closed loop to heat exchangers within wet bench tools that require elevated temperatures for wafer processing solutions. PHW skids include a gas-fired boiler, pumps, filters, expansion tank, water treatment chemical feeder and controls to supply heating water at the flow rate and temperature required by the facility
Configuration Options:
- Flow rates from 200 gpm to 300 gpm
- Supply pressures from 20 psig to 100 psig
- 2 MMBTU to 5.4 MMBTU heat output capacity
- Output temperatures up to 203°F (95°C)
- Multiple redundant pump arrangements
- Variable Frequency Drive (VFD) pump control
- Powder-coated structural steel skid
- Welded carbon steel piping
- Expansion tank and chemical addition feeder
Control System Options:
- Programmable Logic Controller (PLC) or Relay Controls
- Automatic supply pressure and temperature control
- Common trouble alarm dry contacts for remote alarm notification
- Ethernet LAN communication for PLC controls
DI Water Heating is a heat exchanger package delivering hot DI water to wet bench tools that require direct filling or dosing of process solutions with DI water at an elevated temperature. The skid includes a titanium plate and frame heat exchanger, flow control valves and temperature controller. This system exchanges heat from a Process Hot Water (PHW) supply and a DI Water source.
Configuration Options:
- Flow rates from 20 gpm to 40 gpm
- Output temperatures up to 185°F (85°C)
- Titanium plate and frame heat exchanger
- PVDF piping
- Welded polypropylene skid
Control System Options:
- Programmable Logic Controller (PLC) or Relay Controls
- Automatic supply pressure and temperature control
- Common trouble alarm dry contacts for remote alarm notification
Process Utility Monitoring Systems monitor key parameters (e.g. pressure or flow rate) for critical process utilities such as Compressed Dry Air (CDA), Nitrogen (N2) and process water. Measured values and alarms can be displayed locally or remotely.
Air Dryer Automation Systems (ADAS) are supervisory controllers that monitor the Compressed Dry Air (CDA) supply to the facility and operates redundant compressor / dryer units at maximum efficiency. Facilities have two or more air compressor and dryer units to guarantee uninterrupted process tool operation. ADAS distributes load to air dryers based on time and alarms, thus reducing on-line time and service costs, and yielding significant electrical power savings. ADAS places redundant units on stand-by during periods of low CDA demand. It will also rotate the lead and lag status of each unit on a user definable schedule, so that operating hours can be evenly distributed among all units. ADAS will notify facility personnel of alarm conditions, and make emergency responses such as opening a back up Nitrogen supply line in the event of complete compressor or dryer failure.
|
Configuration Options:
- Two (2), three (3) or more compressor / dryer arrangements
- Compressor and Dryer status monitoring
- Dryer alarm monitoring
- High and low line pressure monitoring
- Dew point monitoring
- CDA Flow rate
- Open/closed status of actuated valves for receiver tanks and prefilters
- Cooling water flow and temperature
Control System Options:
- Fully automatic Programmable Logic Controller (PLC) operation
- Ethernet LAN communication for PLC controls
- Human Machine Interface (HMI) color touch screens from 6 to 15 inches diagonal
- Common trouble alarm dry contacts for remote alarm notification
- Alarm history logging
- Building Management System (BMS) integration
|